The Scientific Research Behind Porosity: A Comprehensive Overview for Welders and Fabricators
Understanding the elaborate mechanisms behind porosity in welding is important for welders and producers aiming for flawless workmanship. As metalworkers explore the midsts of this phenomenon, they discover a world governed by different elements that influence the formation of these small gaps within welds. From the composition of the base materials to the intricacies of the welding process itself, a wide variety of variables conspire to either exacerbate or alleviate the visibility of porosity. In this comprehensive overview, we will certainly unwind the science behind porosity, exploring its effects on weld top quality and introduction progressed methods for its control. Join us on this trip through the microcosm of welding blemishes, where accuracy fulfills understanding in the search of perfect welds.
Understanding Porosity in Welding
FIRST SENTENCE:
Evaluation of porosity in welding discloses essential understandings into the honesty and quality of the weld joint. Porosity, defined by the visibility of tooth cavities or gaps within the weld metal, is an usual concern in welding processes. These gaps, otherwise correctly resolved, can compromise the structural stability and mechanical properties of the weld, leading to prospective failings in the ended up product.
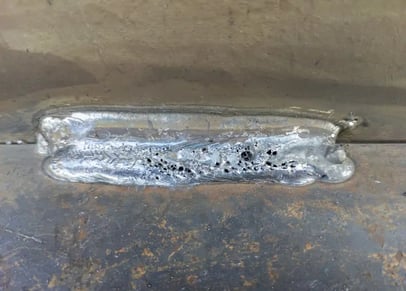
To spot and quantify porosity, non-destructive testing techniques such as ultrasonic screening or X-ray assessment are commonly utilized. These strategies enable the recognition of interior flaws without endangering the honesty of the weld. By examining the size, form, and circulation of porosity within a weld, welders can make enlightened choices to improve their welding processes and achieve sounder weld joints.
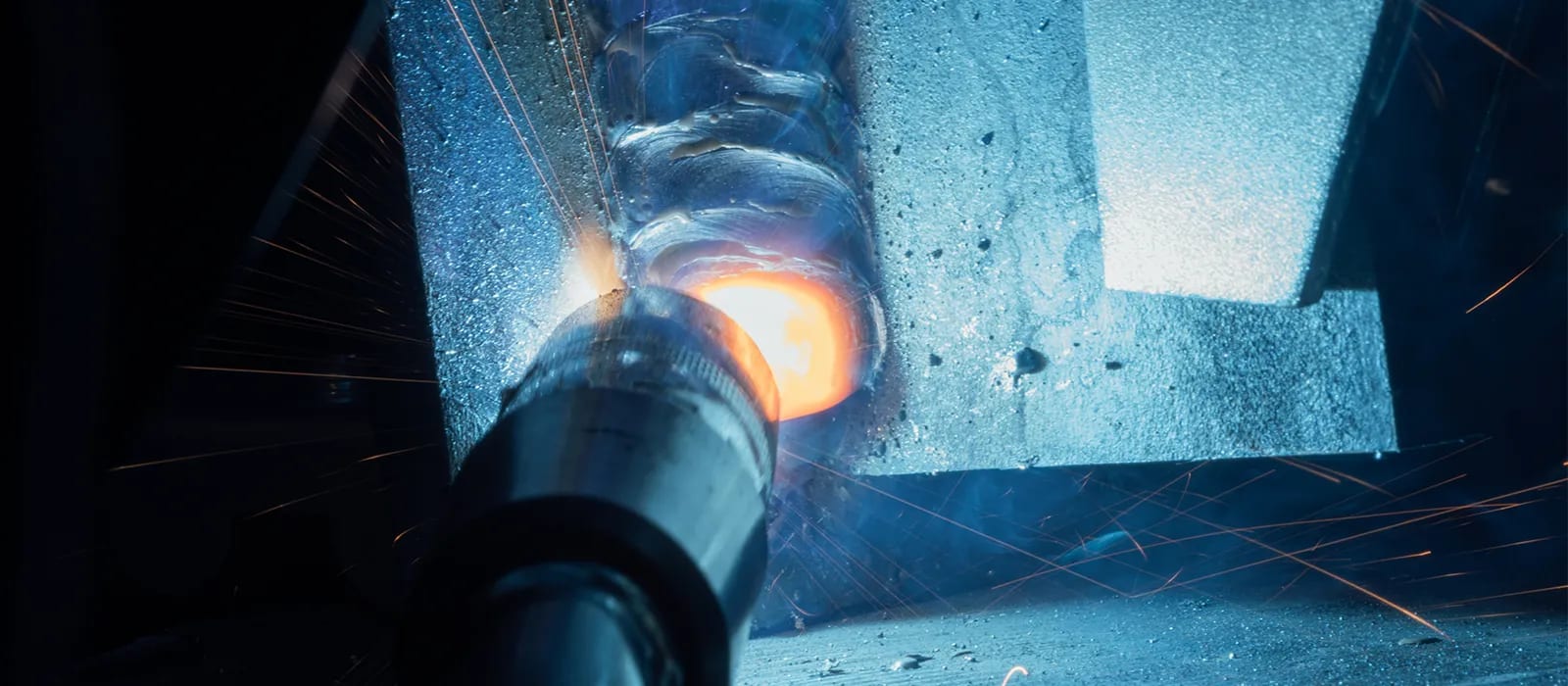
Elements Influencing Porosity Development
The incident of porosity in welding is affected by a myriad of variables, ranging from gas protecting performance to the complexities of welding specification setups. Welding parameters, including voltage, existing, travel rate, and electrode kind, likewise influence porosity formation. The welding method used, such as gas metal arc welding (GMAW) or protected steel arc welding (SMAW), can affect porosity development due to variations in heat distribution and gas protection - What is Porosity.
Results of Porosity on Weld Quality
The visibility of porosity additionally damages the weld's resistance to deterioration, as the caught air or gases within the voids can respond with the surrounding environment, leading to degradation over time. In addition, porosity can impede the weld's capability to stand up to pressure or influence, additional jeopardizing the total high quality and reliability of the bonded structure. In essential applications such as aerospace, auto, or structural building and constructions, where safety and security and durability are paramount, the damaging effects of porosity on weld top quality can have serious consequences, stressing the significance of lessening porosity through correct welding techniques and treatments.
Methods to Minimize Porosity
To boost the high quality of welded joints and make certain structural honesty, welders and producers use details techniques focused on minimizing the formation of spaces and cavities within redirected here the material during the welding process. One reliable method to lessen porosity is to guarantee appropriate product preparation. This includes comprehensive cleansing of the base metal to remove any type of impurities such as oil, oil, or wetness that can add to porosity formation. Furthermore, making use of the suitable welding specifications, such as the proper voltage, existing, and take a trip rate, is crucial in protecting against porosity. Preserving a constant arc size and angle throughout welding additionally helps lower the possibility of porosity.

Making use of the suitable welding technique, such as back-stepping or read here utilizing a weaving movement, can additionally assist disperse warm equally and reduce the chances of porosity formation. By executing these strategies, welders can effectively reduce porosity and produce high-grade bonded joints.

Advanced Solutions for Porosity Control
Carrying out sophisticated innovations and cutting-edge techniques plays an essential function in accomplishing exceptional control over porosity in welding processes. Additionally, using sophisticated welding methods such as pulsed MIG welding or modified ambience welding can also help minimize porosity concerns.
An additional sophisticated solution entails the usage of advanced welding tools. For example, making use of tools with built-in attributes like waveform control and advanced source of power can enhance weld quality and decrease porosity dangers. The execution of automated welding systems with specific control over parameters can substantially lessen porosity flaws.
Moreover, integrating sophisticated tracking Continue and evaluation modern technologies such as real-time X-ray imaging or automated ultrasonic screening can help in finding porosity early in the welding procedure, enabling for immediate restorative activities. On the whole, incorporating these sophisticated solutions can greatly boost porosity control and improve the general high quality of welded components.
Verdict
To conclude, comprehending the science behind porosity in welding is necessary for welders and makers to create top quality welds. By determining the variables influencing porosity formation and applying strategies to lessen it, welders can improve the total weld quality. Advanced remedies for porosity control can even more enhance the welding process and ensure a solid and reliable weld. It is vital for welders to constantly enlighten themselves on porosity and execute ideal methods to attain optimum outcomes.